- Overview
- Design review
- Pre-swirl-rotation
- Vorticity
- Velocity Distribution
Pumping stations
Overview
To ensure optimum pumping station efficiency, pumps must operate in an environment free from air entrainment, vorticity and excessive pre-swirl rotation. Failure to suppress adverse hydraulic phenomena of this type can lead to poor pump performance, accelerated mechanical wear and in extreme cases pump failure. Computational Fluid Dynamics (CFD) can assess flow patterns within a pumping station and give a good assessment of hydraulic performance.
Design review
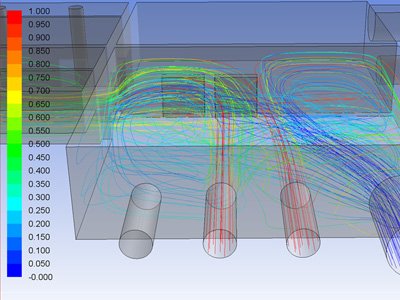
Computational Fluid Dynamics (CFD) can offer a cost effective method of assessing the performance of a pumping station. CFD provides an effective means of evaluating a design produced in accordance with industry standard guidelines. In arrangements where site constraints dictate a departure from a conventional design approach to the layout, CFD modelling can quickly identify, compare and develop alternatives.
Pre-swirl rotation
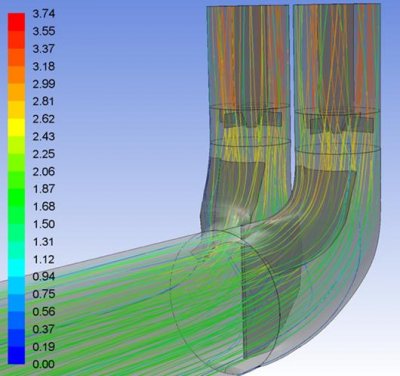
The performance of all rotodynamic pumps will vary with a change in the direction of the impeller inlet velocity vector. Normally, pumps are designed to operate with uniform axial inflow to the pump suction flange. Any swirling or rotational flow effects upstream of the pump will induce a degree of pre-rotation or pre-swirl at the impeller inlet. Computational Fluid Dynamics (CFD) can assess the magnitude of pre-swirl rotation on approach to the pump impeller.
Vorticity
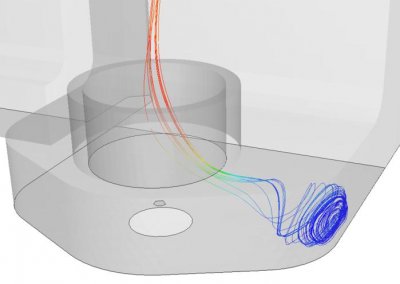
Bulk circulation generated within a wet well as a result of the non-uniform distribution of flow from an inlet can lead to the formation of both free surface and submerged vortices. If sufficiently intense, air may be entrained in the vortex core and transported to the pump impeller, where it may result in mechanical imbalance, increased vibration and cavitation. Computational Fluid Dynamics (CFD) can identify the mechanism for vorticity within a wet well. However, it should be noted that a steady state CFD model cannot accurately predict the intensity, or frequency of vorticity.
Velocity distribution
The variation in velocity distribution on approach to a pump impeller can lead to vibration issues, acceleration of mechanical wear on bearings and seals and, in the case of propeller type impellers, result in potential fatigue and premature blade failure. Computational Fluid Dynamics (CFD) can assess intake conditions on approach to the pump impeller and identify the variation in velocity distribution. The data may be presented as a combination of streak line plots and velocity contours at any given plane within the intake arrangement.